Don’t wait until a malfunction to schedule essential stretch wrap machine repair services.
Don’t wait until a malfunction to schedule essential stretch wrap machine repair services.
Blog Article
A Comprehensive Strategy to Attending To Stretch Wrap Device Fixing Difficulties
You understand that stretch wrap makers are critical for maintaining effectiveness in product packaging procedures. Concerns can arise that disrupt efficiency. What are the finest methods to assure your machines run smoothly?
Understanding Common Stretch Cover Maker Issues
When you depend on stretch wrap devices for efficient packaging, it's crucial to identify usual problems that can interrupt operations - stretch wrap machine repair. One prevalent trouble is irregular tension, which can lead to poor covering and endangered tons stability. If you notice the movie isn't sticking correctly, check for damaged rollers or inappropriate setups
An additional problem you might face is movie breakage, often brought on by incorrect film kind or maker malfunctions. Regularly check the machine for indicators of deterioration to prevent this.
In addition, watch on movie build-up or jams, which can halt manufacturing. Frequently, this takes place because of imbalance or particles in the maker.
Lastly, incorrect sealing can lead to lots coming apart throughout transit. Make sure your machine is calibrated appropriately to maintain the stability of your plans. By remaining attentive and dealing with these issues quickly, you can assist in smoother operations.
The Relevance of Routine Preventative Maintenance
Normal precautionary maintenance is crucial for keeping your stretch wrap equipment running smoothly and effectively. By regularly examining and servicing your devices, you can detect potential issues before they intensify right into pricey repair services. This proactive method not only extends the life-span of your machine however likewise assures that it runs at peak performance.
You must set up normal inspections to clean, lube, and change used parts. Keeping your maker adjusted aids keep excellent wrapping quality, decreases waste, and improves performance. In addition, documenting maintenance activities develops a trusted history that can inform future choices.
Don't neglect the value of training your team on maintenance ideal techniques. When every person recognizes how to care for the device, you lessen the danger of operator mistake bring about failures. Basically, committing to routine preventative upkeep is a wise investment that repays in lowered downtime and boosted performance in your operations.
Troubleshooting Techniques for Quick Repairs
Effective troubleshooting strategies can significantly minimize downtime when your stretch wrap equipment comes across issues. Is the machine not wrapping properly or is it making unusual sounds?
Following, examine the equipment's settings and controls; occasionally, a basic adjustment can settle the issue. Evaluate the film stress and placement, as incorrect setup can cause wrapping failures. Do not forget electrical connections; loosened or damaged wires can disrupt capability.
If you're still facing difficulties, think about running analysis tests if your device has that capacity. Don't wait to seek advice from with a technician if you can't deal with the problem swiftly.
Educating Operators for Effective Equipment Use
To ensure your stretch wrap machine operates at peak efficiency, appropriate training for drivers is necessary. When operators understand the machine's functionalities, they can optimize its possible and minimize downtime.
Encourage them to practice under supervision, resolving any kind of questions or problems they may have. Frequently scheduled refresher courses can maintain their skills sharp and help them adapt to any kind of updates or modifications in technology.
In addition, instill a culture of liability by encouraging operators to report issues or suggest renovations. This positive strategy not only boosts their self-confidence but additionally contributes to the total performance of your operations. With trained operators, you'll see less mistakes and increased efficiency, ensuring your stretch wrap maker continues to be a beneficial asset.
Constructing a Strong Interaction Network In Between Teams
Trained drivers can only do at their finest when there's a strong interaction network between groups. Effective interaction eliminates misunderstandings and warranties everyone's on the exact same web page concerning machine operations and repair service demands. Motivate normal check-ins and conferences to go over problems, share understandings, and address issues.
Using technology, like messaging applications or collaborative platforms, can boost real-time communication, making it less complicated to report problems and share updates quickly. Designating clear functions and responsibilities cultivates responsibility, enabling staff member to reach out to the ideal person when problems emerge.
Furthermore, developing an open atmosphere where everybody feels comfy sharing comments can bring about innovative solutions. By focusing on interaction, you're not simply boosting maker efficiency; you're additionally constructing a cohesive team that works with each other seamlessly. This joint spirit ultimately leads to quicker fixings and decreased downtime, profiting the entire procedure.
Purchasing Quality Replacement Components
When it concerns preserving your stretch cover devices, buying top quality substitute parts is important next for guaranteeing trusted performance and reducing downtime. Economical choices might seem appealing, but they frequently cause more significant problems down the line, costing you more out of commission and lost performance. By choosing top notch components, you're not just repairing a problem; you're improving the overall effectiveness of your tools.
In addition, quality parts are typically made to stricter standards, which suggests they'll fit far better and function even more dependably. This lowers the likelihood of unforeseen breakdowns, enabling your operations to run smoothly. Trusted distributors typically supply guarantees, providing you tranquility of mind in your financial investment.
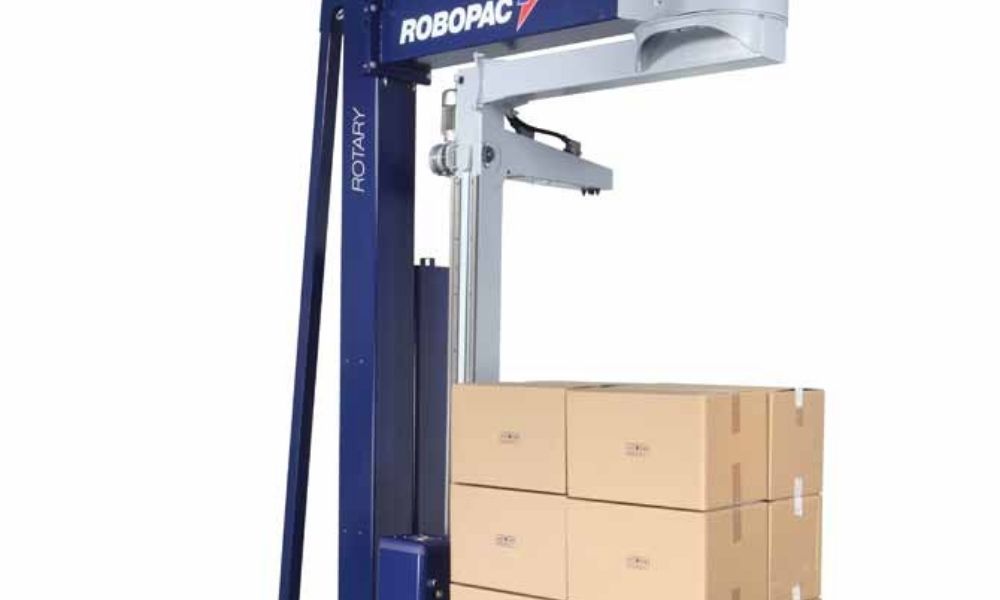
Analyzing Performance Information for Continual Enhancement
To enhance your stretch wrap machine's performance, you need reliable information collection methods. By examining performance metrics, you can pinpoint areas for enhancement and increase performance. Recognizing these possibilities not only improves procedures yet also lowers downtime and repair service expenses.
Information Collection Techniques
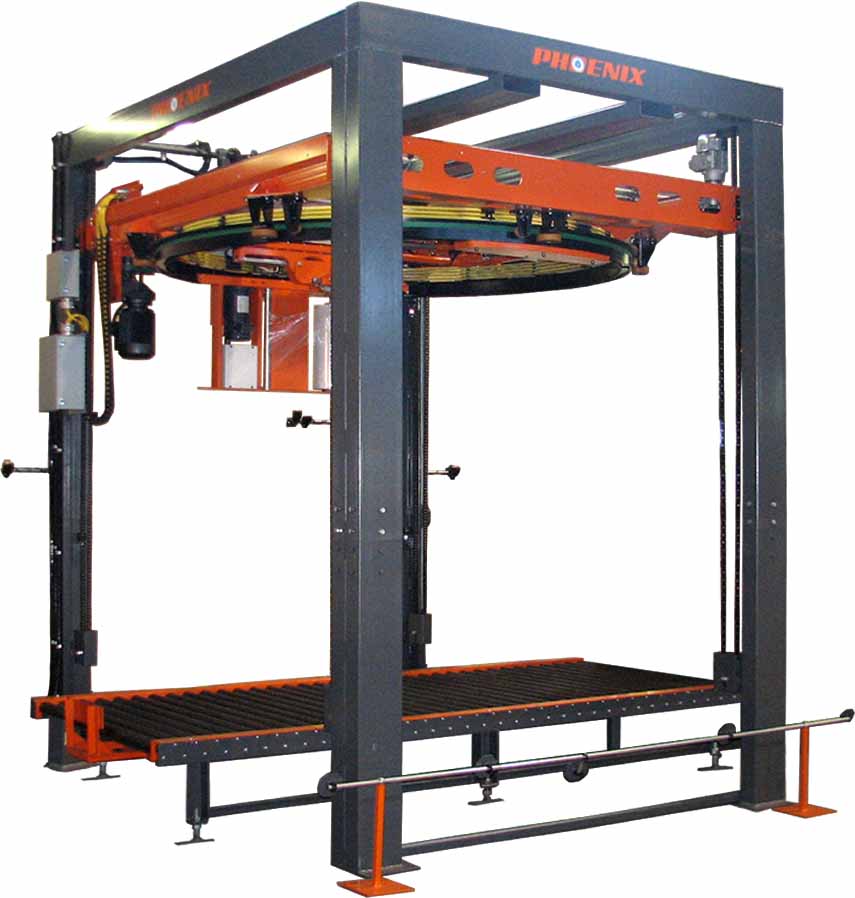
Performance Metrics Evaluation
While examining performance metrics, it's critical to focus on details data points that directly influence your stretch cover maker's efficiency. Begin by tracking cycle times, as they expose how rapidly your maker runs under normal problems. This constant evaluation helps boost productivity, minimize expenses, and inevitably enhance your device's long life, leading to an extra efficient wrapping operation in general.
Determining Renovation Opportunities
As you evaluate performance data, you can reveal useful improvement possibilities Check This Out that improve your stretch wrap machine's performance. Look for fads in downtime, cycle times, and wrap top quality. If frequent breakdowns associate with specific operating conditions, you can change processes to mitigate these issues.
Often Asked Questions
Exactly How Can I Tell if My Maker Requirements a Repair Work or Simply Maintenance?
To inform if your maker requires repair service or simply upkeep, pay attention for uncommon sounds, look for irregular performance, and check for visible wear. If concerns continue after upkeep, it's likely time for a fixing.
What Is the Typical Life Expectancy of a Stretch Cover Machine?
The average life-span of a stretch cover machine is generally five to 10 years, depending upon use and maintenance. Routine care can extend its life, so watch on efficiency and address issues immediately.
Exist Particular Brands Understood for Better Reliability?
Yes, some brands are understood for their integrity. You'll find that firms like Signode and Lantech commonly obtain positive reviews - stretch wrap machine repair. Researching customer responses can aid you pick a dependable stretch wrap device for your demands
What Are the Indicators of Poor Driver Training?
If you notice frequent errors, inconsistent covering, or safety cases, those are indicators of bad operator training. Lack of recognizing about device functions or failing to comply with procedures can greatly affect efficiency and safety.
How Can I Discover a Qualified Service Technician for Fixes?
To find a qualified professional for repair services, request for suggestions from sector peers, inspect on the internet testimonials, and verify certifications. You could also take into consideration speaking to local devices distributors that typically have actually trusted professionals handy.
Verdict
To sum up, taking on stretch wrap device repair service obstacles requires a proactive method. Do not neglect the importance of solid communication straight from the source between teams and continuous evaluation of device outcome.
Report this page